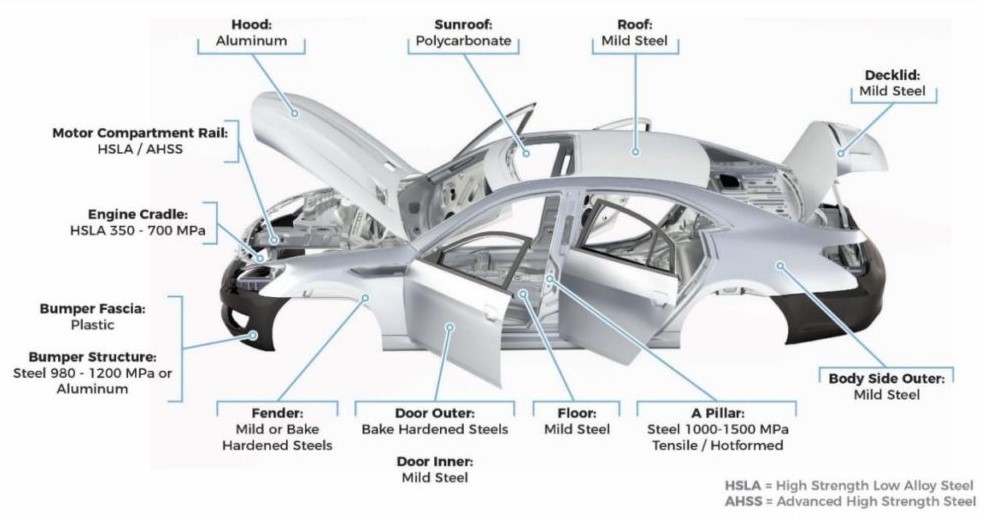
OBJECTIVES:
- COB1: To impart knowledge on the structure, properties, phase diagrams and applications of materials so as to identify and select suitable materials for various engineering applications.
- COB2: To study about the structure, properties and applications of various materials like ferrous, non-ferrous and its alloys.
- COB3: To give insight in to non-metallic materials such as polymers, ceramics and composites.
- COB4: Impart the students to investigate, analyze and provide solutions using heat treatment process and strengthening mechanism.
- COB5: To develop knowledge on the mechanical properties of materials through various testing procedures in engineering field.
OUTCOMES:
On completion of the course the students should be able to:
- CO1:identify various phases of metals and alloys through appropriate phase diagrams, describe the structure of materials, defects and suggest suitable engineering materials for different application
- CO2:evaluate the effect of alloying elements, properties and application of ferrous and non-ferrous metals
- CO3:apply advanced materials such as polymers, ceramics and composites in product design
- CO4:select and apply appropriate heat treatmentprocess and strengthening mechanisms to modify the mechanical behaviour of various materials
- CO5:Evaluate the mechanical behavior of materials for different applications
COURSE CONTENT
MODULE I - CRYSTALLOGRAPHY, CONSITITUTION OF METAL AND METAL ALLOYS
Fundamentals, Crystal structure – Types, Crystal imperfections, Grain size,
Constitution of alloys, Lever Rule, Solid solutions-substitutional and interstitial.
Phase diagrams - Isomorphous, eutectic, peritectic, eutectoid and peritectoid
reactions, Iron – Iron carbide equilibrium diagram, Development of
Microstructure in Iron–Carbon Alloys.
MODULE II - FERROUS AND NON FERROUS METALS
Plain carbon steel and cast iron – classification, microstructure, properties and applications. Effect of alloying additions on steel (Mn, Si, Cr, Mo, V Ti & W). Stainless steel, tool steels, HSLA and Maraging steel - properties and applications, Copper and its alloys. Aluminium and its alloys, Magnesium and its alloys, Titanium and its alloys – microstructure, properties and applications.
MODULE III - NON-METALLIC MATERIALS
Properties and Applications of various Engineering Polymers, Properties and
applications of various Ceramics, Composites and their types, properties and
applications
MODULE IV - HEAT TREATMENT AND STRENGTHENING MECHANISMS
Fundamentals, Classification of processes - Full annealing, normalizing,
Hardening and tempering of steel. Isothermal transformation diagrams,
Continuous Cooling Transformation Diagrams. Case hardening processes -
carburising, nitriding, cyaniding, carbo nitriding, Flame and Induction
hardening. Grain size strengthening, Solid solution strengthening, strain
hardening, yield point phenomenon, dispersion strengthening, fibre
strengthening, precipitation strengthening.
MODULE V - MECHANICAL PROPERTIES AND TESTING
Mechanism of plastic deformation, slip and twinning, types of fracture. Testing
of materials: ASTM standards, Metallographic Examination, Hardness tests,
Impact test Tension test, Wear test, Fatigue test and Creep test.